Logan Brown


Democratization of Metal Fabrication Through a Novel Electrochemical Machining Process
It is difficult and costly to manufacture parts from high-strength metals, especially when creating complex shapes. Difficult to machine metals like hardened steel, tungsten carbide, and nickel-based superalloys are needed for important technologies like farming robots, medical implants, and rocket engines.
​
I designed and built a machine capable of manufacturing precise, complex metal parts at a low cost. This innovative approach avoids common manufacturing problems, costs ten times less than alternatives, and offers enhanced capabilities. My machine can create functional parts from nearly any conductive material, regardless of its mechanical properties, and craft delicate components that other methods would destroy.
​
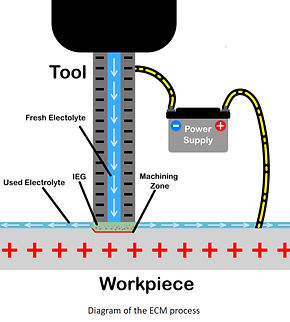
The goal of this project was to create a machine capable of creating metal parts by removing metal electrochemically. In order to meet my goal, the machine had to meet 4 criteria:
-
Machine must effectively remove byproducts from the interelectrode gap (IEG) at a rate sufficient to prevent passivation
-
Machine must have a tool, or multiple tools that are capable of selectively removing material from target areas in a way that is useful for the production of parts. The tool geometry must not impede electrolyte flow.
-
Machine must be capable of maintaining an IEG distance of less than 100μm
-
Machine should be able to filter and recycle its electrolyte
​
The system consists of 4 primary sections:
-
Machine
-
Pump
-
Filtration
-
Control system

PUMP - A critical component of the ECM machine is the electrolyte pump. Existing pumps are expensive and difficult to modify and did not meet design requirements. I designed and built my own peristaltic pump. More than 10 iterations were needed to meet all design criteria.​
​

-
Pump must withstand corrosive electrolyte.
-
Easy to control flow rate or pressure in software.
-
Achieve high pressure to drive electrolyte through a small needle.
-
Inexpensive to produce and maintain.
-
Easy to modify and change properties. ​
FILTRATION - ECM uses electrolyte at a rapid rate which cannot be reused without filtration. Iron hydroxide slurry also passes through and/or clogs most filters, making filtration difficult. To solve this, I created a filtration system that can continuously filter electrolyte slurry without clogging.
​

-
Continuous filtering of electrolyte slurry without clogging
-
High flow rate to supply machine continuously. (16 l/h)
-
Easy to clean and maintain.
-
Inexpensive to produce, operate, and replace. ( < 20$ )
-
Has no moving parts.

CONTROL SYSTEM - Repurposing a 3D printer control board was impractical due to a lack of programming access to some ports on the microcontroller. Because of this, I designed my own control board PCB using KiCAD and wrote my own custom firmware.
​


As there is relatively little existing research and technology available relating to my project, it is composed of almost entirely original work. I created all of the components of the project myself except for the machine frame which came from a 3D printer, and the power supply which was an off-the-shelf variable power supply. A few of the components I made include the control board, the electrolyte pump, the firmware, and the filter.
Additionally, much of the machining process is new, with only the basic idea of using a tight gap between electrodes that is flushed with electrolyte being based on the literature. To my knowledge, the use of a CNC tool to make partial depth cuts by sweeping along a surface has not been done with an ECM machine before. I also did not find any sources using conducive homing to detect the position of the part.
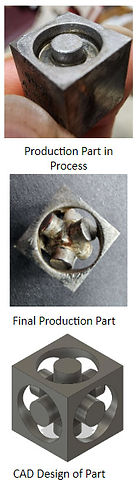
